Beam clamps are designed to be used in applications where a load is placed on a structural beam (such as an I beam, universal beam, H beam, RSJ). They attach to the lower flange of a structural beam and allow for secure fixing without the need for welding and drilling. The most widely available beam clamps are called girder clamps and they can be very useful for circus rigging if you are intending to hang apparatus as a direct vertical load.
However, in the circus industry we usually prefer to set up aerial apparatuses on pulley systems. The pulley system will have a working point (where you clip apparatus to) and an anchor point (where the end of the rope is tied off to). Connecting these two points is rope that runs through pulleys above both the working point and the anchor point.
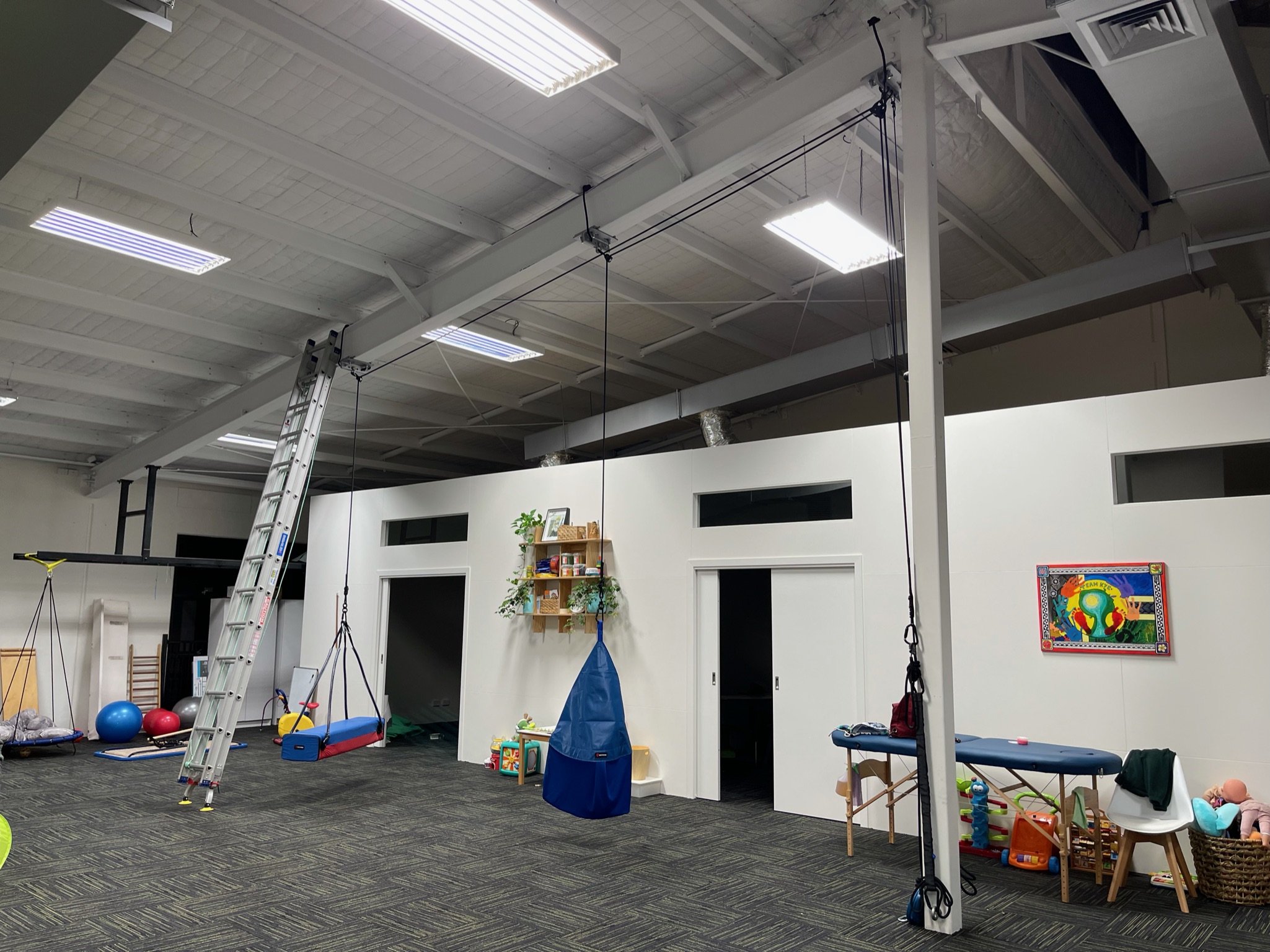
Rigging this way is beneficial for the following reasons:
- Easy change of apparatuses.
- Easy change of heights.
- The potential to install a safety belay system to rescue aerialists in distress.
- The potential to add a mechanical advantage system to allow the aerialist to be lifted into the air (great for training/teaching situations and great for performance effects).
This type of system adds additional loads to the horizontal roof structure it is attached to. It is not a suitable system to install in every scenario as you need a strong horizontal beam, strong supporting vertical beams, suitable anchor points and the approval of a structural engineer. The span of the horizontal beam and the age of the building will have a great deal of influence as to whether a pulley system can be safely installed in your studio.
Sadly, the girder clamp mentioned above is NOT designed to be used in pulley systems. The girder clamp is designed only for direct vertical loads. Pulley systems, as described above, involve lateral as well as vertical pull.
Until recently, beam clamps specifically engineered and designed for pulley systems in circus applications were not available. Circus riggers have been obliged to rig these systems on rigging slings, on self-assembled clamps made from scaffolding supplies, by welding cleats to the beam or by drilling into the beam. These options vary in effectiveness, safety, cost and ease of installation. They all represent, historically, the only available options for installing pulley points onto structural I beams.
Because of the lack of circus-specific solutions to this ongoing rigging problem, Trix Circus developed the Engineer-Certified Aerial Beam Clamp. These are purpose built for the expected loads of high-level circus technique and the specific applications of circus rigging.
Trix Circus Engineer-Certified Aerial Beam Clamps
Each Trix Circus Beam Clamp unit is made up from four separate sections and bolted onto the lower flange of a structural beam using four 16mm Nyloc bolts tightened to a torque of 90kN. They are neat and waste very little vertical height.
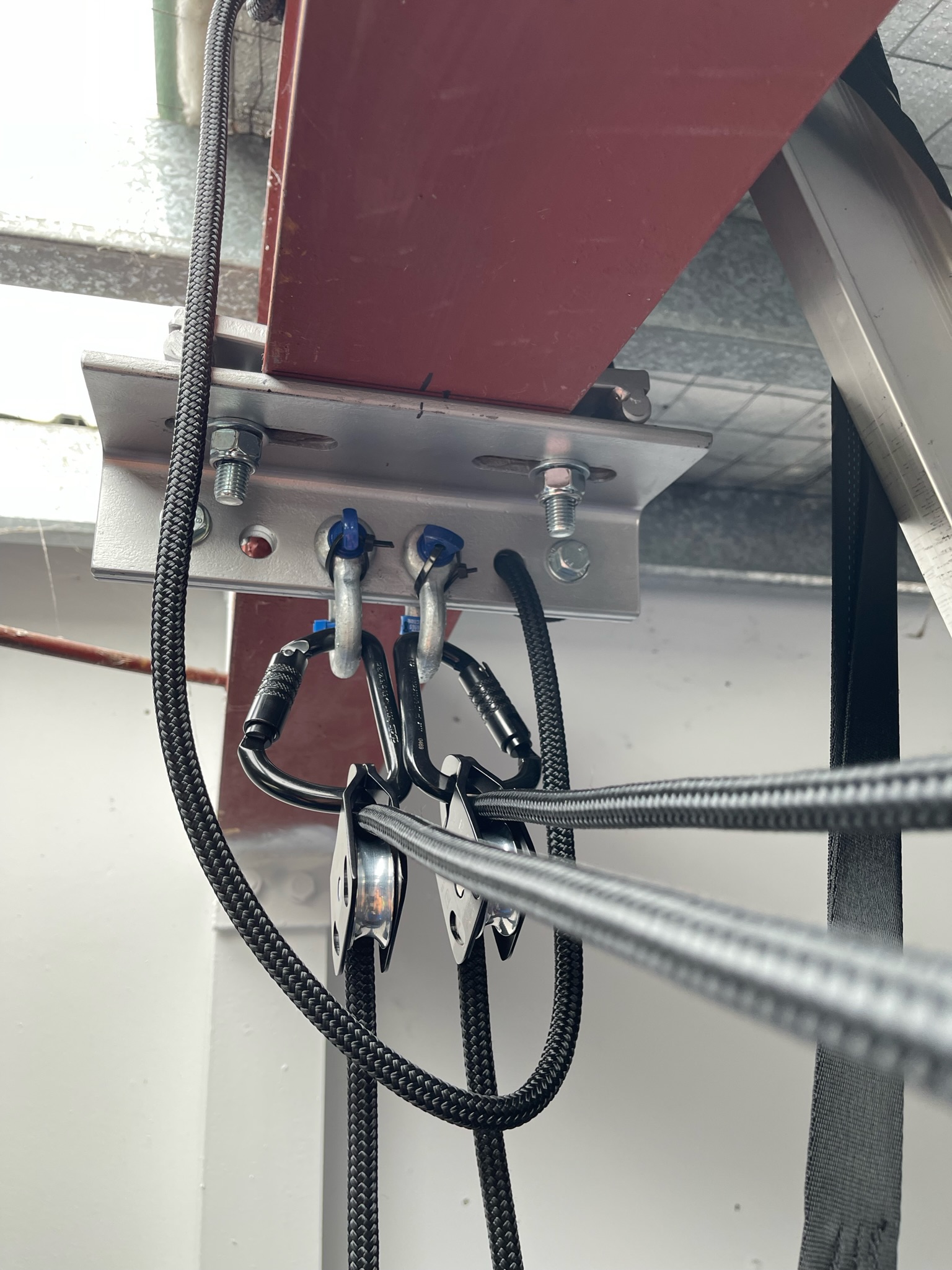
These beam clamps are:
- Designed specifically for circus applications. This means you are installing a piece of kit that is operating within its INTENDED USE. This is good for your insurance and will reduce your liability.
- Designed specifically for human loading.
- Designed specifically for pulley systems (designed to take loads at a 90 degree angle).
- Designed for even loading of the structural beam.
- Designed without costly welding for critical anchors.
- Designed for strength and durability.
- Designed to be highly versatile; each has four holes to rig from. The two centre holes can each hold a weight of 1500kg. The two outside holes are designed for lightweight rigging use (non human loading) and can hold a weight of 500kg.
- Designed with a combined Working Load Limit (WLL) is 3000kg and a Minimum Breaking Strain (MBS) is 6000kg.
- Designed as semi-permanent installations that have flexible positioning. You can move these clamps into the positions you need. Which means as your studio evolves, your rigging can move around to suit new developments.
- Designed for ease of installation: no need for drilling and welding into the beam.
- They are engineered and certified, reducing your liability and ensuring the safety of your business and your clients.
- They are made to Australian Standards (AS 4100 and AS 4991.2004), reducing your liability and ensuring the safety of your business and your clients.
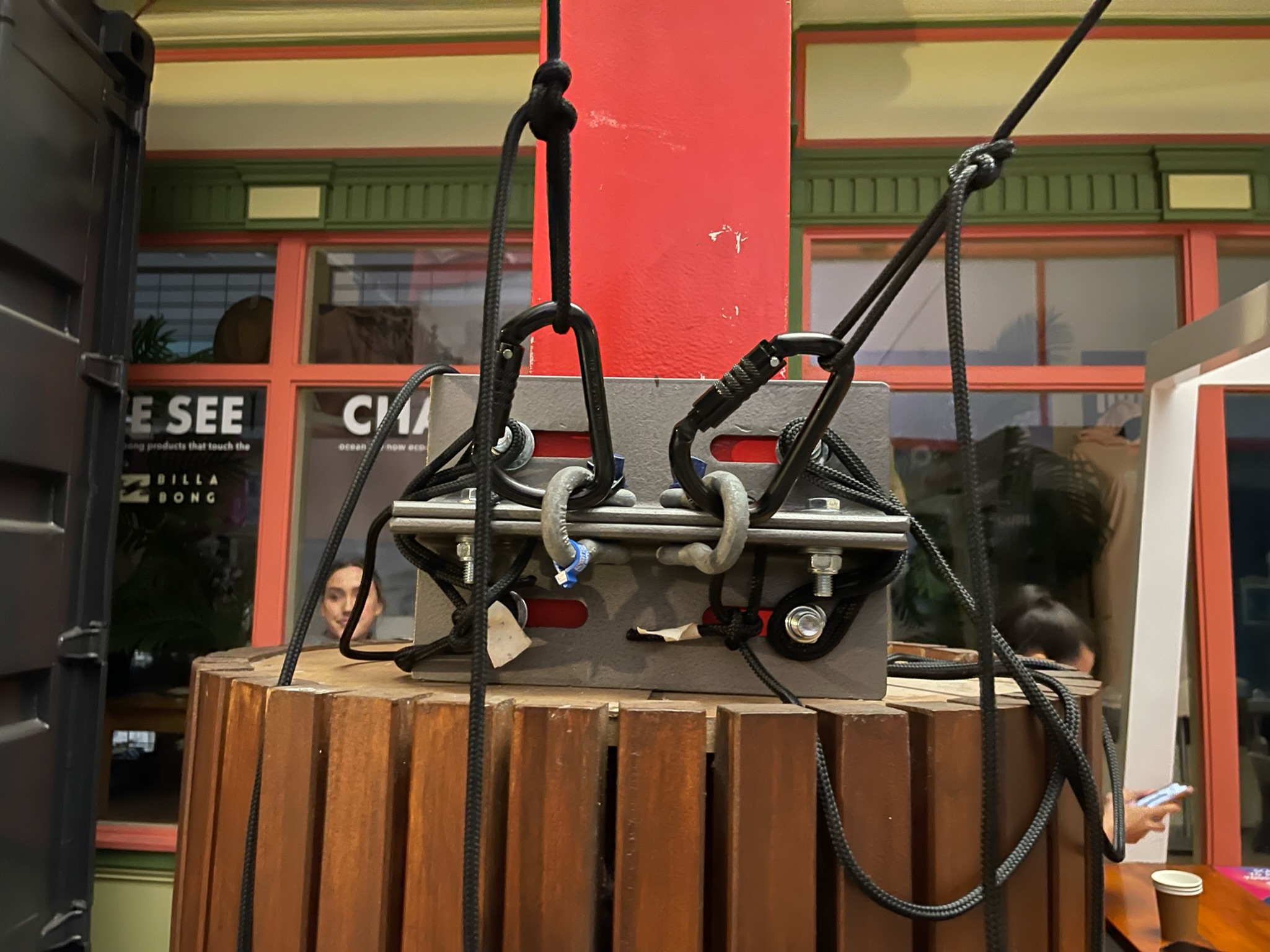
Trix Circus Beam Clamp in use as a haul away/paging anchor. The Trix Circus Beam Clamp is designed as a horizontal column anchor, it can only be used as a vertical column anchor with a suitable redundancy (eg. a secondary Trix beam clamp).
Other Options Commonly Used to Rig Pulley Systems
Drilling into the beam and using eye nuts
- Drilling is not always permitted by engineers in charge of the installation.
- Landlords often do not want permanent changes to the beams made by drilling.
- Drilling into an I beam is physically difficult for the installers.
- Eye nuts lack versatility; there is only one available rigging point and once installed, it cannot be moved without leaving a permanent hole.
- Not all available eye nuts are designed to be used in circus-style pulley systems (they must be designed for use with a 90 degree load).
- They lack redundancies; there is only one bolt in place keeping the eye nut connected.
- Eye nuts drilled into an I beam will always mean that the rigging will not be centered to the webbing. Ideally, your load should be centered under the webbing of the beam and as evenly distributed as possible.
- If choosing to use eye nuts, make sure that you use collared eye nuts that are suitable for use at a 90 degree angle and have manufacturer’s specifications that indicate what torque (Nm) the eye nut must be tightened to. The addition of witness marks and an additional safety rope for redundancy is also recommended. The eye nut must also be installed flush to the flange of the beam.
Leaving the beam unaltered is better for the insurance of the engineers and building owners.
Welding permanent lugs/cleats
- Suitable access for hot-works is not a simple process and is not always possible when dealing with structural beams high in the roof.
- In order for your welding to be engineer certified it must be designed by an engineer and welded to the specified Australian Standard by a welder qualified in the welding processes outlined in the design plans. It can be very difficult (and expensive) to source a welder who is both qualified to weld to the correct Australian Standard, is willing to come onsite and is licensed and insured to work/weld at heights.
- Landlords often do not want permanent changes to the beams made by welding.
Leaving the beam unaltered is better for the insurance of the engineers and building owners.
Using rigging slings
Rigging slings aren’t always the safest solution over beams. The sharp edges of the beams can be padded to protect the slings but this works best with a direct vertical load. When a pulley point is rigged on slings, the slings will always drag along the beam laterally, making it difficult to rig the point accurately and putting greater wear and tear on the sling itself.
According to Australian Standards (AS/NZS1891.4) slings also must be inspected (by both sight and by touch) by the user before and after every use, which is difficult to do when they are installed in a roof. According to AS/NZS4497.1 the slings must also be inspected every 3 months by a competent, trained and accredited person. This means that your rigging inspections will need to be quarterly (instead of twice yearly as specified by the engineer certification for the Trix Circus Beam Clamps). This will greatly increase your costs over time.
Using self-assembled scaffolding beam clamps
This clamping system is assembled from pieces of 48mm scaffolding pipe and Gravlock scaffold clamps. It has been a useful stop-gap to avoid rigging on synthetic slings and before the arrival of engineer-certified circus-specific beam clamps. However, this system has a lot of limitations.
- It consists of materials specifically designed for temporary installations.
- It is not designed for scenarios with consistent lateral pull (with a load pulling at a 90 degree angle) as is the case with a pulley system.
- Testing has proven that these self-assembled beam clamps slip when loaded beyond 1224kg.
- Using the scaffolding clamps in this manner loads the clamps unevenly. This can result in the clamps slipping under constant dynamic use and could lead to catastrophic failure.
- This installation lacks engineering controls. There is no manufacturer’s guide to install these clamps for this purpose.
- It has not been specifically designed for human loading in a circus application.
- It will not be covered by any manufacturer’s insurance or liability as the clamps and pipe that make up this system are being used outside of their intended use.
Realistically, your decision about which of these systems to utilise will come down to risk assessments from qualified personnel, the types of structures you have in your roof and walls, the height of the studio, the accessibility of your structures, the location of your studio, the availability of qualified contractors, your own willingness to take on risk, your budget, as well as other determining factors. We encourage you to purchase and install (using a qualified rigger) beam clamps from Trix Circus as they have been designed exactly with circus use in mind, reducing your risk, reducing your liability and reducing your headaches.
Trix Circus Aerial Beam Clamp facts:
-
- Engineer designed by an RPEQ.
- Certified and manufactured to the engineer’s specifications.
- Engineer certified to meet the demands of circus applications and forces.
- Meets Australian Standard 4100 – Steel Structures and AS 4991.2004 – Lifting Devices.
- They are designed to withstand a load between vertical and 90 degrees in line with the supporting beam.
- Slot holes are mitred into the connecting face to allow the clamp to be used on beams ranging between UB150 to UB530.
- They are also suitable for use on pitched/angled and vertical beams.
- They are highly versatile; each has four holes to rig from. Two holes are located on either side of the centre web of the structural beam and can each hold a weight of 1500kg. The two outside holes are designed for lightweight rigging use (non human loading) and can hold a weight of 500kg.
- They have a combined Working Load Limit (WLL) of 3000kg.
- They have a combined Minimum Breaking Strain (MBS) of 6000kg.
- Available rigging holes fit standard rated 2 tonne shackles.
- All bolts use nyloc nuts and are tightened to a torque of 90kN (engineer’s specifications).
- 4x bolts providing overall compression of the beam without unevenly loading the clamp
- 4x individual bolts which provide multiple redundancies (in comparison to other clamps that rely solely on dual fasteners or eye nuts with unique connections and lack redundancies).
Other Aerial Beam Clamps
There are other clamps designed for aerial use out on the market. These vary in quality of design and manufacture.
Our recommendation is to always purchase clamps:
- That have been designed by a qualified engineer.
- That have been manufactured by a qualified manufacturer.
- That have built-in redundancies.
- That do not overload one side of the clamp..
- Have 4 + points of contact that grip the beam as a whole.
- To install a redundancy. Wherever possible, install a separate rope system around the beam, clamp and pulley in case of system failure.
Thanks for reading and safe rigging!